High Speed Research Compressor
Projekthistorie
Der HSRC ist der größte Verdichterprüfstand am LTF und wird seit 2016 in Kooperation mit GE Aerospace betrieben. Sein einzigartiges Design ermöglicht die experimentelle Untersuchung der letzten Hochdruckverdichterstufen in einem skalierten Testrig unter strömungsmechanisch triebwerksrepräsentativen Bedingungen.
Prüfstandsaufbau
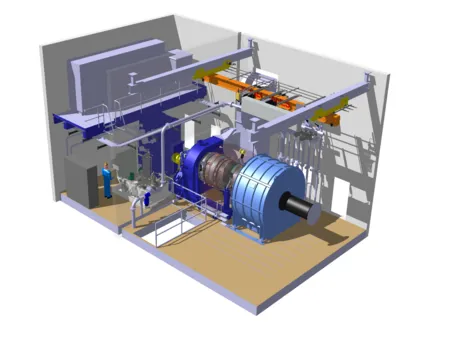
Der 3,5-stufige Axialverdichter wird von einem 3-MW-Elektromotor angetrieben. Über ein Getriebe mit einer Übersetzung von 1:2,52 wird eine maximale Verdichterdrehzahl von 5.000 U/min erreicht. Ein Massenstrom von bis zu 30 kg/s durchströmt den Verdichter.
Die Massenstrommessung erfolgt über einen in-situ kalibrierten Einlauf. Eine Beruhigungskammer mit einem Durchmesser von ca. 3 m sorgt für eine homogene Anströmung des Verdichters.
Zur Erstellung des Verdichterkennfelds kann der Prüfling mittels einer druckseitigen Drossel bis zum Strömungsabriss angedrosselt werden. Mithilfe instationärer Gehäusedrucksensoren wird ein globaler Strömungsabriss automatisch erkannt. In diesem Fall wird die Drossel innerhalb von <1 s schlagartig geöffnet, wodurch starke strukturelle Belastungen des Testrigs vermieden werden.
Das Sekundärluftsystem (SAS) erlaubt die gezielte Steuerung der Leckageströmungen durch die Rotordichtungen. Darüber hinaus ermöglicht die kontrollierte Kühlung des Rotors und des zweischaligen Gehäuses eine Einstellung des Rotorspalts im kleinen Maßstab. Zur Stabilisierung des Verdichters kann am Rotor 3 Zapfluft entnommen werden.
Das bis zu 200 °C heiße Abgas wird über einen Schalldämpfer in die Umgebung abgegeben.
Instrumentierung
Fest installierte Sensorik
Zur Analyse des Prüflings und zur Überwachung des Prüfstandbetriebs kommt eine Vielzahl fest installierter Sensoren zum Einsatz. Diese dienen sowohl der Betriebspunktüberwachung und Effizienzbestimmung als auch der Gewährleistung eines sicheren Betriebs. Die Effizienz des Verdichters wird über das Druck- und Temperaturverhältnis zwischen Ein- und Auslass sowie über Drehmoment- und Drehzahlmessung an der Antriebswelle bestimmt.
Zum Einsatz kommen unter anderem:
- ca. 600 Scannivalve-Drucksensoren (verschiedene Messbereiche)
- ca. 300 Temperatursensoren (NI, mit eigener Cold Junction)
- ca. 30 instationäre Gehäusedrucksensoren (Kulites)
- ca. 700 Beschleunigungs-, Näherungs- und weitere Sensoren
- Torqmeter zur Drehzahl- und Drehmomentmessung
- MTU BSSM zur Überwachung des Rotorspalts
- 3 Umgebungsdrucksensoren
- Rotordaten-Telemetriesystem
- Bis zu 75 Dehnungsmessstreifen zur Schwingungsüberwachung an Rotoren und Statoren
Insgesamt stehen mehr als 1.600 Messkanäle zur Verfügung.
Traversierbare Instrumentierung
Am HSRC können bis zu drei Strömungssonden hinter jeder Schaufelreihe installiert und in drei Achsen traversiert werden (radial, Umfangsrichtung, Rotation in Gier-Richtung). Die Auswahl der Sonden erfolgt je nach Messanforderung.
Besonders die Möglichkeit zur instationären Messung des Strömungsfeldes mit 48 kHz (Druckmessung, 4-Sensor FRAP) und bis zu 100 kHz (Temperatur und Massenstromdichte mit 5 mm Hitzdraht-Sonden) bei repräsentativen Machzahlen und starker Instationärität hinter den Rotoren stellt ein alleinstellungsmerkmal des Prüfstandes dar.
Verfügbare traversierbare Messtechnik:
- 2 kombinierte Fünflochsonden mit Totaltemperaturmesskopf
- 3 konventionelle Fünflochsonden
- 6 CTA-Messkanäle für Hitzdrahtmessungen (Dantec)
- 1 FRAP-Sonde mit 4 Sensoren (48 kHz Aufnahmefrequenz, Limmat)
Anwendung
Am HSRC werden neue Konzepte und Technologien zur Stabilisierung der hinteren Hochdruckverdichterstufen unter triebwerksrepräsentativen Machzahlen getestet. Diese Untersuchungen erfolgen in enger Zusammenarbeit mit GE Aerospace.
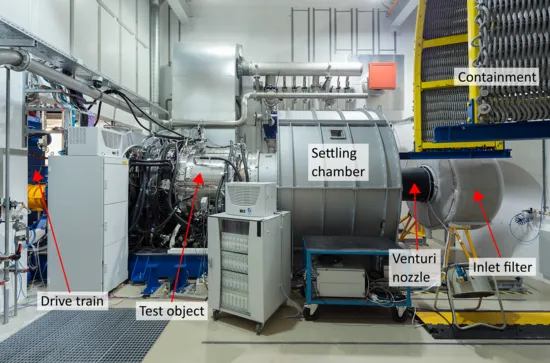
Projekthistorie
- 2013: Projektstart mit Definition der Konstruktionsanforderungen für den Verdichterprüfstand
- 2015: Inbetriebnahme der ersten Subsysteme
- 2016: Erste Inbetriebnahme des Verdichters bei Auslegungsdrehzahl, In-situ-Kalibrierung der Einlaufdüse, Überprüfung der homogenen Anströmung
- Seit 2016: Jährliche Testkampagnen mit kontinuierlicher Weiterentwicklung
Kooperation
Das Projekt wurde vom Bayerischen Wirtschaftsministerium, der Technischen Universität München und GE Global Research in Garching, Deutschland, in Zusammenarbeit mit GE Power, GE Aviation und GE Oil & Gas finanziert.
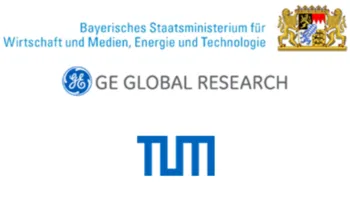