FogeLRaP – Development of a filling strategy optimization for a true to dimension lightweight RTM tool using process simulations
In this project, a virtual design tool for the reduction of tool weight and the optimization of filling strategies in RTM processes is developed.
Project Partners
Grunewald GmbH & Co. KG, HÜBERS Verfahrenstechnik Maschinenbau GmbH
Duration
01.03.2021 – 31.08.2023
Funding authority
Federal Ministry for Economic Affairs and Energy
Motivation
For the increasing production rates in the civil aviation industry, the resin transfer molding (RTM) process is gaining further importance and is expected to become more widespread with the results of this project. The greatest current challenges for wider use are, on the one hand, the production of geometrically complex components that meet the high requirements for aerospace tolerances. On the other hand, the development of the optimal gating strategy, the positioning of inlets and outlets is one of the main problems for the reproducible production of components of the highest quality. Furthermore, pure resin areas in radii or dry spots caused by resin flow in the edges are main criteria for part scrap. Therefore, the goal in this project is to avoid such defects and reduce scrap by linking compaction and filling process simulation.
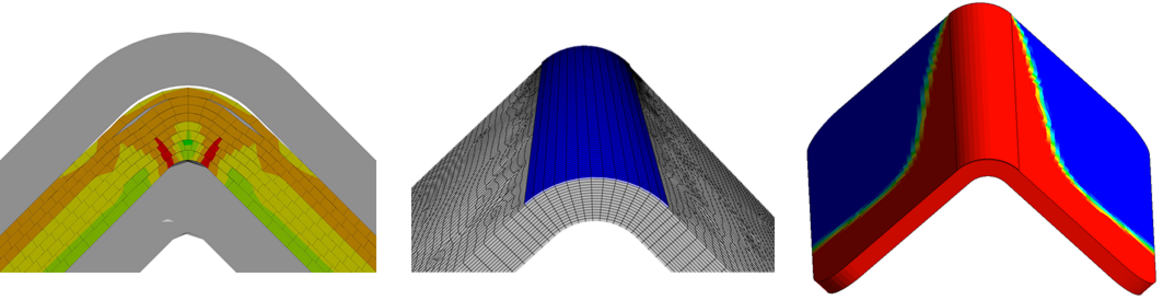
Method
In the project, an efficient compaction simulation is developed to calculate the mold forces and the preform geometry. Furthermore, an automated tool for generating the filling simulation with consideration of the compaction results will be developed. The diagram shows the method used in the project for the process simulation chain using the example of an L-section. First, a compaction simulation is carried out, which allows the prediction of the distribution of final fiber volume content. Cavities which are not filled by the preform in the mold are modeled as flow channels in a next step. In the subsequent filling simulation, the influence of so-called race-tracking channels, which occur for example in narrow mold radii, is taken into account. With the aid of an automated virtual process chain based on sensor data, the current flow front position in the tool is measured and an optimum filling strategy is determined. This method makes it possible to react in the process to varying preforms in terms of initial thickness or position in the mold and thus reduce scrap.