Um die Ziele für eine umweltfreundliche Luftfahrt zu erreichen, muss die Luftfahrtbranche nicht nur für die Endprodukte, sondern auch für deren Fertigung energieeffiziente und ressourcenschonende Lösungen finden. Faserverbundwerkstoffe wie carbonfaserverstärkter Kunststoff (CFK) bieten ein enormes Leichtbaupotential für Strukturbauteile von Fluggeräten, was deren Umweltverträglichkeit steigert. Etablierte Fertigungsverfahren für CFK-Bauteile sind allerdings geprägt von einem hohen Energiebedarf, der beispielsweise bei der Kühlung der vorimprägnierten Halbzeuge (Prepregs) und der Aushärtung im Autoklav entsteht.
Die Universität Bayreuth und die Technische Universität München zielen daher im Verbundvorhaben „InLineCon“ auf eine Material- und Prozessentwicklung ab, mit der die für duroplastische Systeme nötigen Schritte der Kühlung der Prepregs und der Konsolidierung im Autoklaven überflüssig werden. Hierbei wird ein strahlungshärtendes und thermisch schnellhärtendes Harzsystem bzw. die Kombination zu dualhärtenden Formulierungen hergestellt, wobei die für Prepregs übliche energieintensive durchgehende Kühlkette bei -18 °C entfällt. Als Fertigungsverfahren dient das in der Luftfahrt etablierte Automated Fiber Placement (AFP). Anlage und Prozess werden in InLineCon so modifiziert, dass in Verbindung mit dem neu entwickelten Harzsystem eine In-Line-Konsolidierung direkt im Ablagewerkzeug möglich wird. Durch ein entsprechendes Temperatur- und Druckprofil kann dabei die für Faserverbundwerkstoffe nötige Prozesszeit im Autoklav minimiert oder sogar vollständig vermieden werden.
Das Projekt wird über das nationale Luftfahrtforschungsprogramm (LuFo) des Bundesministeriums für Wirtschaft und Energie (BMWi) gefördert.
Aktuelles
Grundlagenforschung zur Direktkonsolidierung duroplastischer Prepreg-Tapes mittels Automated Fiber Placement
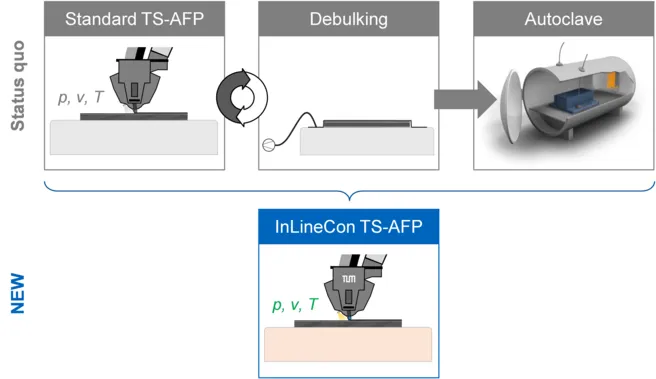