EMOTION – Enhanced Mould for Thermoplastic Fuselage in and out of Autoclave Consolidation
Das Projekt EMOTION stellt ein Werkzeug bereit, das die Herstellung von Rumpfhalbschalen aus thermoplastischem Faserverbundwerkstoff für hohe Stückzahlen ermöglicht. Das Werkzeug kommt im CS2 Verbundprojekt STUNNING zum Einsatz. Des weiteren werden Möglichkeiten der Prozessierung außerhalb eines Autoklaven untersucht.
Projektpartner
ALPEX GmbH, Ostseestaal GmbH & Co KG, Topic Leader: NLR - Netherlands Aerospace Centre
Laufzeit
01.09.2019 – 01.03.2022
Fördergeber
EU HORIZON 2020 – Clean Sky 2 Joint Undertaking
Motivation
Zuerst wird ein Werkzeug mit ca. 4m Durchmesser und 8m Länge zur Herstellung einer Rumpfhalbschale entwickelt und gefertigt. Die Prozesskette sieht vor, dass 2D erstellte Laminate maschinell gegriffen und im Werkzeug platziert, mittels Vakuumsack in ihrer Position gesichert und im Autoklaven unter Druck und bis zu 400°C konsolidiert werden. Die hohen Verarbeitungstemperaturen stellen im Bereich der Wärmeausdehnung, folgend Verzug der Faserarchitektur und des Bauteils insgesamt, als auch beim Energieverbrauch, eine Herausforderung dar. Der Einsatz unterschiedlicher Legierungen und ein teilflexibler Unterbau sollen hier neue Lösungsansätze zur Industrietauglichkeit entwickeln. In einem zweiten Schritt werden Technologien zur Konsolidierung außerhalb eines Autoklaven an einem Werkzeugteilsegment untersucht. Energieeinsparung, reduzierter Einsatz von Hilfsstoffen und somit Kosteneinsparung, soll die Wettbewerbsfähigkeit der Industrie stärken. Die Entwicklung und Bereitstellung eines Werkzeuges mit ca. 4m Durchmesser und 8m Länge zur Herstellung einer Rumpfunterschale soll die entwickelten Lösungsansätze nachweisen.
Vorgehen
Ostseestaal, spezialisiert auf die Umformung großer Metallbauteile und Formen, liefert die Grundstruktur des Werkzeuges. Der Werkzeugentwickler und –bauer Alpex verarbeitet diese zum einsatzfähigen Werkzeug weiter. Die TUM unterstützt mit Material-und Prozesswissen und Vorversuchen den Entwicklungs- und Designprozess. In der Konzeptphase werden im Verbund unterschiedliche Lösungswege untersucht und Risiken durch begleitende Versuche bewertet und minimiert. Die erste Projektphase schließt mit Test und Übergabe eines voll skalierten Werkzeuges zur Herstellung eines Rumpfschalensegmentes ab. Im zweiten Projektteil wird ein neuartiges Werkzeugkonzept entwickelt, das die Anforderungen einer Konsolidierung ohne Autoklav erfüllen soll. Die Prozessentwicklung basierend auf Direktkonsolidierung und Nachkristallisation mittels heizbarem Werkzeug erfolgt an der TUM. Auf Grund des Entwicklungsrisikos, erfolgt die Umsetzung an einem Ausschnitt bzw. Segement des großen Werkzeuges.
Zusammenfassung des Projektes
Das EMOTION-Projekt wurde Ende Februar 2022 erfolgreich abgeschlossen. Die TUM möchte sich bei den Projektpartnern ALPEX und Ostseestaal für die erfolgreiche Zusammenarbeit herzlich bedanken. Ein besonderer Dank geht auch an das NLR als Topic Manager, das für die Themenfindung und die Koordination mit verbundenen CleanSky 2 Projekten, sowie der Eignungsprüfung und Demonstration des neu entwickelten Werkzeugs verantwortlich war. Einen Überblick über den Projektfortschritt gibt die untenstehende öffentliche Zusammenfassung. Sie können sich gerne an die TUM oder einen der Projektpartner wenden, wenn Sie mehr über Hochtemperaturwerkzeuge für die Herstellung von thermoplastischen Verbundwerkstoffen erfahren möchten.
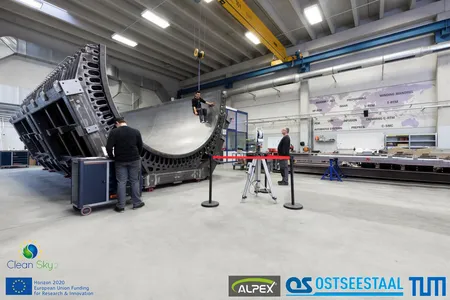
Das EMOTION Projekt stellt ein Werkzeug zur Verfügung, das die Herstellung von großvolumigen Halbschalen aus thermoplastischem Faserverbundwerkstoff ermöglicht. Das Werkzeug wird im Rahmen des CS2 Gemeinschaftsprojekts STUNNING eingesetzt, das einen Beitrag zum Multifunktionsrumpfdemonstrator (MFFD) leistet.
Verbundwerkstoffstrukturen werden für die neueste Generation von Verkehrsflugzeugen verwendet. Eine weitere Verbesserung der Leichtbaustruktur der Flugzeugzelle soll durch den Einsatz von thermoplastischen Verbundwerkstoffen erreicht werden. Während die Verwendung von Kohlenstofffasern als festes und steifes Material beibehalten wird, sollen die Matrixmaterialien auf Thermoplaste umgestellt werden. Dieser Wechsel ist auch durch die potenziell verbesserten Eigenschaften am Ende des Lebenszyklus motiviert, was z. B. eine bessere Recyclingfähigkeit bedeutet.
Leichte Strukturen sind für den umweltfreundlichen Betrieb von Flugzeugen und allgemein von Mobilitätsanbietern von entscheidender Bedeutung. Weniger Gewicht bedeutet, dass mehr Passagiere oder Fracht bei gleichem CO2-Fußabdruck transportiert werden können. Neue Antriebstechnologien werden diesen Bedarf an Leichtbaustrukturen nicht ersetzen. Vielmehr erfordern die Elektrifizierung und die Wasserstofftechnologie im Bereich der Antriebe weitere Verbesserungen im Leichtbau, um die geringere Energiespeicherdichte zu kompensieren. Thermoplastische Verbundstrukturen werden aus mehreren dünnen Lagen gestapelt, die zu einem festen und starken Material verfestigt bzw. konsolidiert werden müssen. Konsolidierung bedeutet, dass ein Druck von bis zu 10 bar und eine Temperatur von bis zu 400°C auf das gestapelte Material ausgeübt wird. Dazu wird ein formgebendes Werkzeug benötigt, das der Temperatur und dem Druck eines Autoklaven (AC) standhält.
Das EMOTION Konsortium erforscht die Haltbarkeit und die Prozesseignung wie Temperatur und Konsolidierungsdruck mit dem Ziel, das beste Zusammenspiel zwischen Werkzeug und Bauteil zu erreichen. Während der Herstellung des Bauteils wird der Verbundwerkstoff bei Raumtemperatur positioniert, muss aber später zur Konsolidierung auf 400 °C erhitzt werden. Sowohl das Werkzeugmaterial (in der Regel Metall) als auch der Verbundwerkstoff dehnen sich während dieses Vorgangs aus und schrumpfen. Der Unterschied im thermischen Verhalten verursacht die Herausforderungen. Im schlimmsten Fall widersteht das Metallwerkzeug der Temperatur, aber die hergestellte Verbundstoffstruktur wird durch Faltenbildung beeinträchtigt. Falten in der Faserarchitektur verringern die Festigkeit eines Verbundwerkstoffs. Daher sucht das EMOTION Projekt nach einer Lösung und stellt eine Werkzeuglösung bereit, die die Verstärkungsfasern perfekt ausgerichtet hält.
Kohlenstofffaserverbundwerkstoffe selbst verursachen aufgrund ihrer energieintensiven Herstellung einen relativ hohen CO2-Fußabdruck. Durch die Verwendung von thermoplastischen Matrixmaterialien steigen die Verarbeitungstemperaturen an, weshalb energieeffiziente Verarbeitungstechnologien erforderlich sind, um einen Gesamtvorteil in Bezug auf den ökologischen Fußabdruck zu erzielen.
Das EMOTION-Projekt ist daher in einen kurzfristigen und einen mittelfristigen Technologieansatz unterteilt. Die Verarbeitung in einem AC ist Stand der Technik und kann zu einer besseren Konsolidierung führen. Die Verarbeitung außerhalb eines AC (ooA) zielt auf eine Energieeinsparung ab, wodurch thermoplastische Verbundwerkstoffe noch wettbewerbsfähiger werden und einen geringeren ökologischen Fußabdruck hinterlassen.
Das EMOTION-Projekt hat am Ende gezeigt, dass beide Ansätze auf denselben technologischen Schlüsseln aufbauen können 1) Verwendung spezieller Legierungen für die Werkzeughaut, um die Ausdehnungsunterschiede zwischen Werkzeug und Bauteil auszugleichen, 2) Multi-Material-Werkzeugdesign, das in der Lage ist, mit inhomogenen Wärmeausdehnungen umzugehen. Beide bilden auch die Grundlage für ein induktiv beheiztes Werkzeugsystem, das den AC Betrieb ersetzen kann.
Während der kurzfristige Ansatz im Rahmen des Gemeinschaftsprojekts STUNNING durch den Einsatz des EMOTION-Werkzeugs für die Herstellung der Außenhaut des multifunktionalen Rumpfdemonstrators demonstriert wurde, hat der größenskalierte mittelfristige Ansatz die grundsätzliche Machbarkeit einer induktiv beheizten Schalenform nachgewiesen. Weitere Forschungsarbeiten sind erforderlich, um Verbundwerkstofflaminate zu qualifizieren, die unter Bedingungen mit Temperaturgradienten konsolidiert werden. Es sind weitere Entwicklungen erforderlich, um den mittelfristigen Ansatz auf ein robustes und zuverlässiges industrielles Niveau zu heben.
Danksagung
The project is made possible by the support of the European Union within the framework of the HORIZON 2020, Clean Sky 2 programme.
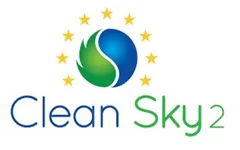
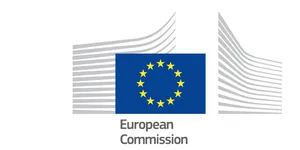
Ansprechpartner
Dipl.-Ing. Thomas Wettemann; Dr.-Ing. Swen Zaremba