SKR-FVK – Steigerung der Kosteneffizienz und Robustheit in der automatisierten Produktion faserverstärkter Kunststoffbauteile
Charakterisierung und Validierung einer neuen CRTM Prozessvariante, bei welcher der Faservorformling in thermoplastischen Folien gekapselt wird, um Prozesszykluszeiten und Produktionsinvestmentkosten zu minimieren.
Projektpartner
Alpex Technologies GmbH, DEKUMED Kunststoff- und Maschinenvertrieb GmbH & Co. KG, RAC GmbH - Riedmann Advanced Composite, Polymer Competence Center Leoben GmbH, Lehrstuhl für Carbon Composites - Technische Universität München
Laufzeit
01.10.2019 – 30.09.2021
Fördergeber
Bundesministerium für Wirtschaft und Energie (Deutschland) sowie Bundesministerium Digitalisierung und Wirtschaftsstandort (Österreich)
Motivation
Die Industrialisierung von Produktionsprozessen für faserverstärkte Kunststoffe (FVK) ermöglicht es heute, FVK-Strukturen in automobilen klein- bis mittelvolumigen Serien konkurrenzfähig zu fertigen. Prozesszeitenanalysen der hierbei verwendeten Herstellungsverfahren zeigen jedoch, das nicht-wertschöpfende Nebenzeiten, wie z. B. Evakuieren und Werkzeug reinigen, aktuell noch bis zu 30 % der Gesamtprozesszeit ausmachen. Mit dem Ziel der Reduzierung der Prozesszykluszeiten wird im Projekt SKR-FVK eine neue Prozessvariante auf Basis des Compression Resin Transfer Molding (CRTM) Prozesses entwickelt. Der innovative Ansatz des „Film-Sealed Compression Resin Transfer Molding“ (FS-CRTM) Prozesses liegt in der Kapselung des Faservorformlings mit thermoplastischen Folien. Hierbei agiert die Folie als Dichtung, wodurch das Harz während der Injektion nicht mit dem Werkzeug in Kontakt kommt und dessen Verschmutzung komplett vermieden wird. Ebenfalls kann der versiegelte Faservorformling bereits außerhalb des Werkzeugs in einem vorgelagerten Prozess evakuiert werden. Konventionelle Dichtungssysteme werden beim FS-CRTM redundant, wodurch neue Werkzeugkonzepte für die Compositeherstellung entwickelt werden können. Des Weiteren ermöglicht eine optimierte CRTM Prozesssteuerung, auftretende Prozessdrücke zu senken, wodurch eine Produktion mit kostengünstigeren Niederdruckinjektionsanlagen und ohne kostenintensive Pressen ermöglicht wird. Durch die Entwicklung und Erforschung des FS-CRTM Prozesses leistet das Projekt SKR-FVK seinen Beitrag, dass Herstellungsverfahren für FVK zukünftig neben der Klein- und Mittelserie ebenfalls in der automobilen Großserie Einsatz finden.
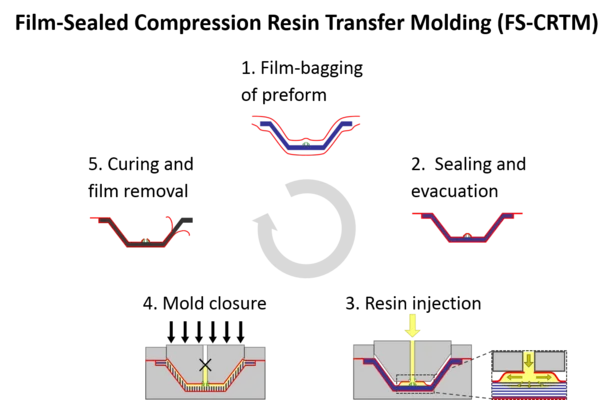
Vorgehen
Im Rahmen des Projektes SKR-FVK wird der Film-Sealed Compression Resin Transfer Molding Prozess an der TUM charakterisiert und dessen industrielle Realisierbarkeit anhand von Laborversuchen sowie Demonstratorherstellung verifiziert. Zu Beginn des Projektes werden dominierende Prozessparameter für eine robuste Fertigung mittels Laborversuchen ermittelt. Der eigens hierfür entwickelte Laborprüfstand ermöglicht es, sowohl die Injektions- als auch die Kompaktierungsphase des FS-CRTM Prozesses nachzubilden und alle wichtigen Prozessgrößen, wie z.B. Injektionsdruck oder Kompaktierungskraft, aufzuzeichnen. Die Kavität ist hierbei aus transparentem PMMA gefertigt, wodurch die Imprägnierung sowohl auf der Preformober- als auch auf der -unterseite mittels Kameras aufgezeichnet werden kann. Eine hierdurch realisierbare optische Prozessüberwachung ermöglicht es ebenfalls, potentielle Ursachen einer unvollständigen Preformimprägnierung, wie z. B. Racetracking, zu untersuchen und Präventionsstrategien durch aktive Flusskontrollmechanismen zu validieren. Im zweiten Teil des Projektes werden zwei- sowie dreidimensionale Demonstratorbauteile mittels einer von Projektpartnern speziell entwickelten Niederdruckinjektionsanlage und einem dynamischen Werkzeugsystem hergestellt. Dieses neuartige Werkzeugsystem ermöglicht eine FS-CRTM Produktion ohne kostenintensive Presse und beinhaltet ebenfalls ein bewegliches Werkzeugkonzept (Schiebertechnologie), durch welches zum einen komplexe Bauteilgeometrien mit z. B. Hinterschnitten hergestellt werden können und zum anderen der Harzfluss im Werkzeug über lokale Preformkompaktierung optimal gesteuert werden kann.
Danksagung
Der Lehrstuhl dankt dem deutschen Bundesministerium für Wirtschaft und Energie (BMWi) für die Projektförderung im Rahmen des "Zentralen Innovationsprogramms Mittelstand (ZIM)" unter der Fördernummer ZF4004314TA9 sowie dem österreichischen Bundesministerium für Digitalisierung und Wirtschaftsstandort für eine Förderung im Rahmen der „Coin- Programmlinie Netzwerke – international“.
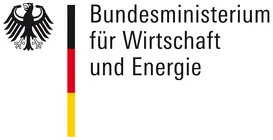

Ansprechpartner
Dr.-Ing. Swen Zaremba