MAI Plast – Entwicklung kosteneffizienter Verarbeitungstechnologien zur automatisierten Prozessierung von thermoplastischen Hochleistungsverbundwerkstoffen für Großserienanwendungen
Thermoplastische Hochleistungs-Faserverbundwerkstoffe kosteneffizient gestalten.
Projektpartner
Audi AG, BASF SE, BMW AG, Siemens AG, SGL Carbon GmbH, Airbus Group Innovations, Thermoplast Composite GmbH, Airbus Helicopters Deutschland GmbH, Premium Aerotec GmbH, KUKA Systems GmbH, Voith Composites GmbH & Co. KG, Universität Augsburg, Fraunhofer-Einrichtung für Gießerei-, Composite- und Verarbeitungstechnik IGCV, Fraunhofer-Institut für Werkzeugmaschinen und Umformtechnik IWU, Deutsches Zentrum für Luft- und Raumfahrt e. V., TEC-KNIT CreativCenter für technische Textilien GmbH, Krauss-Maffei Technologies GmbH
Laufzeit
01.07.2012 – 30.06.2015
Fördergeber
Bundesministerium für Bildung und Forschung
Motivation
Durch grundlegend neue Konzepte im Bedarfsfeld „Mobilität“ haben neue Leichtbau-Technologien, wie beispielsweise der Einsatz von faserverstärkten Kunststoffen (FVK), in allen verkehrstechnischen Systemen zunehmend an Bedeutung gewonnen. Derzeit eingesetzte Bauteile aus FVK werden in überwiegendem Maße mit duromeren Matrixwerkstoffen (Harzen) hergestellt. Die aktuell auf dem Markt verfügbaren Harzsysteme weisen jedoch im Vergleich zu thermoplastischem Matrixmaterial einige Nachteile hinsichtlich Zykluszeit, Energieverbrauch, Lagerzeit und Recyclingfähigkeit auf. Zudem sind die aktuell eingesetzten Fertigungsverfahren häufig durch einen hohen Anteil an manueller Arbeit und einen hohen Zeitaufwand gekennzeichnet. Der alternative Einsatz von thermoplastischem Matrixmaterial ermöglicht daher im Vergleich eine Verringerung der Durchlaufzeiten in der Prozesskette, was die automatisierbare Herstellung der Bauteile sowie effizientere Fügetechniken mit einschließt.
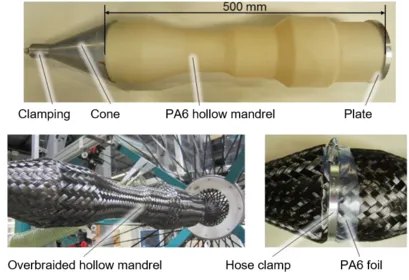
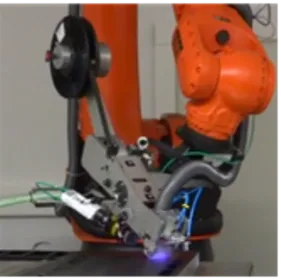
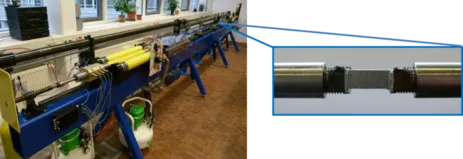
Vorgehen
Der Lehrstuhl für Carbon Composites bearbeitete in diesem Vorhaben drei wesentliche Themenbereiche:
(1) Thermoplastkernflechten: Die Herstellung eines thermoplastischen Hohlbauteils als Kern entspricht ebenso wie die Umflechtechnik mit Carbonfasern dem Stand der Technik. Die wissenschaftlichen und technischen Arbeitsziele lagen daher in folgenden Bereichen:
- Die Wandstärke des Thermoplastkerns musste hinsichtlich Kernstabilität, Faservolumenanteil und Benetzungsverhalten optimiert werden. Die Notwendigkeit zusätzlich eingebrachter Folien in mehrlagigen Bauteilen wurde dabei ebenso betrachtet wie das unterschiedliche Verhalten verschiedener Matrixmaterialien.
- Das Fließ- und Tränkungsverhalten der Matrix während des Konsolidierungsprozesses wurde untersucht, um die Bauteilqualität durch ein optimales Zusammenspiel von Druck, Temperatur und konstruktiven Maßnahmen steuern zu können.
- Der Konsolidierungs- und Umformungsprozess sollte unter Gewährleistung der Maßhaltigkeit stattfinden, ein weiterer Zuschnitt durfte nicht erforderlich sein. Verschiedene Konzepte zur definierten und kontrollierten Umformung wurden daher betrachtet (beispielsweise Sollknickstellen durch konstruktive Maßnahmen oder gezielte lokale Erwärmung). Hierzu wurden verschiedene Heizkonzepte wie beispielsweise Infrarot, beheizte Werkzeuge oder eine Kombination verschiedener Maßnahmen untersucht.
(2) Weiterentwicklung Thermoplast-AFP und ressourceneffizienter Materialeinsatz durch lokale Verstärkungsstrukturen: Die wissenschaftlichen Ziele bei der Erprobung der T-AFP Technologie lagen insbesondere im Verständnis des Zusammenspiels von Konsolidierungstemperatur, Druck und Geschwindigkeit der Anpressrolle sowie der Einfluss dieser Parameter auf die Bauteilqualität, speziell die mechanischen Kennwerte sowie die Porosität. Die Problematik der thermischen Spannungen im Bauteil sollte durch die Untersuchung des Zusammenhangs mit genannten Prozessgrößen besser beherrschbar werden. Die Vermehrung des Prozesswissens, auch hinsichtlich der Verarbeitbarkeit verschiedener Werkstoffe, führte dazu, dass auch bisher unvermeidlicher Verschnitt durch ein Überschwingen der Regelung in Start und Endpunkten des Ablegens minimiert werden konnten. Weiterhin wurde im Projekt gemeinsam mit anderen Projektpartnern aus Automotive und Luftfahrt die ressourceneffiziente Kombination unterschiedlicher Legeverfahren untersucht.
(3) Dehnratenabhängigkeit: Der Lehrstuhl beschäftige sich mit der Ermittlung der für die Crashsimulation im Automotive Sektor benötigen Materialkennwerte. Zum Erlangen von grundlegenden Erkenntnissen zur Schadensinitiierung und Schadensausbreitung in FVK unter Crashbelastung und deren Einfluss auf die Energieabsorption im Bauteil wurden insbesondere folgende Effekte näher untersucht:
- Einfluss der Belastungsgeschwindigkeit auf die verschiedenen intralaminaren Versagensmoden von FVK und somit der Energiefreisetzungsraten für Matrixzug-, Matrixdruckversagen, sowie Faserzug- und Faserdruckversagen.
- Einfluss der Belastungsgeschwindigkeit auf die interlaminaren Versagensmoden, insbesondere des Delaminationsverhaltens unter Mode I (Versagen aufgrund von Normalspannungen in Dickenrichtung) und unter Mode II (Versagen aufgrund von Schubspannung zwischen den Einzellagen des Laminatverbundes).
Hervorzuheben ist, dass für die experimentelle Untersuchung des Delaminationsverhaltens und der Versagensmechanismen unter Crashbelastung in Anlehnung an quasi-statische Normen Versuchstechniken weiterentwickelt und neu entwickelt wurden, da für diesen Belastungsgeschwindigkeitsbereich keine genormten Prüfmethoden zur Verfügung standen.
Publikationsliste
Plöckl, M.; Kuhn, P.; Körber, H.: Characterization of unidirectional carbon fiber reinforced polyamide-6 thermoplastic composite under longitudinal compression loading at high strain rate. 11th International DYMAT Conference, 2015
Danksagung
Der Lehrstuhl bedankt sich für die Förderung des Projektes „Entwicklung kosteneffizienter Verarbeitungstechnologien zur automatisierten Prozessierung von thermoplastischen Hochleistungsverbundwerkstoffen für Großserienanwendungen – MAI Plast“, die vom Bundesministerium für Bildung und Forschung über den Spitzencluster MAI Carbon gewährt wurde (Förderkennzeichen: 03MAI01M).

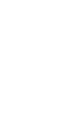
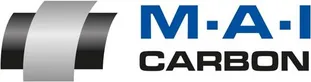
Ansprechpartner
Dipl.-Ing. Kalle Kind; Luciano Avila Gray, M.Sc.; Dr.-Ing. Swen Zaremba
Abschlussbericht
Externer Link (pdf)