COMBO3D – Composite Mould Tool Based on 3D Printing
A thermoplastic RTM mould for the production of a thermoset flaperon is produced using large scale extrusion based additive manufacturing, simulating and integrating surface near active temperature control.
Project Partners
Alpex Technologies GmbH, Leichtmetallkompetenzzentrum Ranshofen GmbH, Victrex Manufacturing Ltd
Duration
01.04.2019 – 30.09.2021
Funding authority
Clean Sky 2 Joint Undertaking under the European Union’s Horizon 2020 research and innovation programme
Motivation
In the past, Additive Manufacturing (AM) has been used for the production of tools and has proven advantages such as cost reductions, faster development cycles, and shorter time to market as well as improved quality through functionalization of the material. These concepts however have only been used for small scale tooling, limited mostly by the building volume available in current 3D printers. With new large scale additive manufacturing these approaches can be scaled up to enable mould production for aerospace parts. However this requires high performance thermoplastics to be printable in a cool environment as. To match the challenging conditions during mould manufacturing and use for part production newly developed high performance PAEK are needed. This allows integrating active temperature control near the surface of the printed tool to improve the cure quality as well as reduce the cycle time.
Method
COMBO3D investigates the additive manufacture a fiber reinforced thermoplastic tool with integrated active temperature control, to shorten the cure cycle time. By using a robot guided large scale fiber reinforced plastics extrusion additive manufacturing process the tool can be produced as a single part, directly integrating the temperature control, shortening the lead-time. Using a robot-guided process also allows to print the final demonstrator tool in one piece in curved layers (real 3D printing), enabling a load path oriented fiber integration and fast restoration of the tool surface to compensate a lower expected lifespan. To ensure tool stability during the curing cycle, carbon fiber reinforced PAEK will be used. Thermal simulation supports the tool design. The design of the tool is optimized by implementing the heating and cooling system in a thermal simulation as well as flow optimization within integrated fluid channels.
Acknowledgement
This project has received funding from the Clean Sky 2 Joint Undertaking under the European Union’s Horizon 2020 research and innovation programme under grant agreement No 831989. This publication reflects only the author’s views and the European Union is not liable for any use that may be made of the information contained therein.
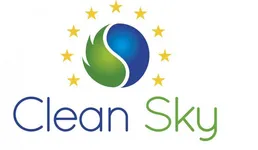
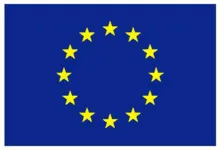
Contact Persons
Patrick Consul, M.Sc.; Matthias Feuchtgruber, M.Sc.; Dr.-Ing. Swen Zaremba