COPRAS – Composite Parts for Rocket Applications with Integrated Sensors
Development, manufacturing, testing and flight of a thermoplastic CFRP rocket module with integrated fiber optic temperature sensors.
Project Partners
German Aerospace Center (DLR), Center of Applied Space Technology and Microgravity (ZARM), European Space Agency (ESA), Swedish National Space Agency (SNSA)
Duration
01.03.2016 – 31.12.2019
Funding authority
Federal Ministry for Economic Affairs and Energy (BMWi)
Motivation
Structural parts of rockets are exposed to substantial mechanical and thermal loads. Research sounding rockets as used in the REXUS program consist of several identical structural modules carrying the scientific payload. The design of a module includes a cylindrical outer shell and thick, monolithic load input rings with a defined assembly interface. Up to now all REXUS modules are made out of aluminum. Reducing the structural weight allows higher payloads, higher apogees or reduced fuel consumption. To achieve this goal a new manufacturing concept using the Thermoplastic Automated Fiber Placement (TP-AFP) process was developed to manufacture a lightweight composite module. In addition, the embedding of fiber optic sensors was to be integrated into the concept to enable component monitoring during operation with a minimum knockdown of the laminate’s mechanical performance.
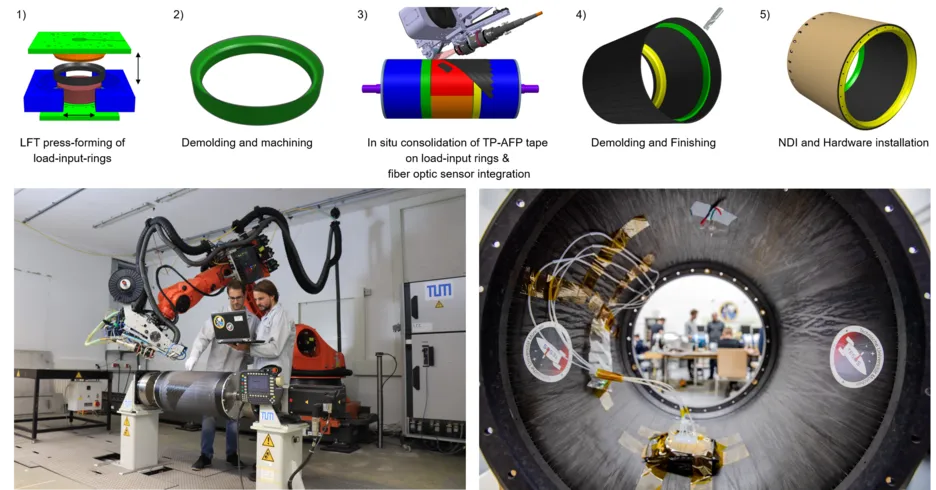
Method
The task of this project was to develop a manufacturing concept for a thermoplastic CFRP module with integrated fiber optic sensors (FOS). This included a structural analysis, qualification and testing of the structure together with an implementation of a FOS measurement system for temperature measurements during flight.The concept comprises two separate manufacturing steps for the load input rings and the cylindrical shell. The rings were manufactured by press-forming of long fiber thermoplastic material (LFT), the shell structure by Thermoplastic Automated Fiber Placement (TP-AFP). TP-AFP allows an in situ consolidation of the shell on the previously manufactured rings without additional adhesive or mechanical fasteners. Polyetheretherketone (PEEK) was chosen as matrix material due to its excellent mechanical properties under thermal loads and its compatibility with the chosen processes.A finite element (FE) structural analysis of the module based on given loading conditions defined the geometrical dimensions of shell, rings and the required joining area. The laminate lay-up was optimized to fulfill the required module stiffness. Coupon level characterization of the LFT and TP-AFP materials at room temperature and service temperature were carried out to obtain input parameters for the structural analysis. Sub component tests of the in situ joint between shell and ring material as well as screw insert pullout tests covered critical aspects of the module design. Full scale tests were performed for a defined spectrum of vibrations and a maximum bending load. Capsuled fiber Bragg grating (FBG) sensors were integrated into the TP-AFP laminate during manufacturing. This allows temperature measurements in between the plies during flight. The experimental payload of the module consists of a fiber optical measurement device to operate the FBGs, electrical reference sensors, a computer for data storage and downlink and a power board. The composite module achieved a weight reduction of more than 40% compared to the aluminum modules. It was launched on March 4, 2019 as a structural part of the REXUS 23 rocket to an apogee of 75.42 km. Beyond sounding rockets, the concept of in situ bonded TP-AFP tapes on complex monolithic LFT structures has many potential applications within aerospace and beyond and will thus be further investigated at the LCC.
Publications
Journal Papers
Engelhardt, R.; Ehard, S.; Wolf, T.; Oelhafen, J.; Kollmannsberger, A.; Drechsler, K.: In Situ Joining of Unidirectional Tapes on Long Fiber Reinforced Thermoplastic Structures by Thermoplastic Automated Fiber Placement for Scientific Sounding Rocket Applications. Procedia CIRP, 85:189-194, 2019, https://doi.org/10.1016/j.procir.2019.09.015
Conference Papers
Engelhardt, R.; Ehard, S.; Oelhafen, J.; Kollmannsberger, A.; Amann, R.; Günzel, P.; Drechsler, K.: Development of a Lightweight Carbon Composite Rocket Module with Integrated Fiber Optical Temperature Sensors as Part of the Experiment "TESOS" on REXUS 23. 24th ESA Symposium on European Rocket & Balloon Programmes and Related Research, 24:271-275, Essen, Germany, 16-20 June 2019, https://www.tib.eu/en/search/id/TIBKAT%3A1687597367/24th-ESA-Symposium-on-European-Rocket-and-Balloon/
Engelhardt, R.; Oelhafen, J.; Ehard, S.; Kollmannsberger, A.; Drechsler, K.: Manufacturing of a Thermoplastic CFRP Rocket Module with Integrated Fiber Optical Temperature Sensors, The 29th Annual International SICOMP Conference on Manufacturing and Design of Composites, Lulea, Sweden, 2018.
Posters
Engelhardt, R.; Oelhafen, J.; Ehard, S.; Kollmannsberger, A.; Drechsler, K.: Manufacturing, Testing and Flight of a Carbon Fiber Reinforced Plastic Rocket Module with Integrated Fiber Optical Temperature Sensors. 2nd Symposium on Space Educational Activities, Budapest, Hungary, 2018.
Others
Sloan, T.: Rocket module manufactured with in-situ consolidation survives first flight test. Composites World, 10/2019, pp. 32-34, https://www.compositesworld.com/blog/post/rocket-module-manufactured-with-in-situ-consolidation-survives-first-flight-test
Mason, K.: A giant leap in rocket weight savings. Composites World, 01/2019, pp. 44-47, https://www.compositesworld.com/blog/post/a-giant-leap-in-rocket-weight-savings
Acknowledgement
The Chair of Carbon Composites would like to thank the German Federal Ministry for Economic Affairs and Energy (BMWi) for funding this work as well as the Mobile Rocket Base (MORABA) department of German Aerospace Center (DLR), the Center of Applied Space Technology and Microgravity (ZARM) and the European Space Agency (ESA) for their support. At the Technical University of Munich, the work was done and supported by Rupert Amann, Luciano Avila Gray, Nicolas Benes, Michael Bösl, Teddy Brault, David Colin, Duc Thien Dinh, Raphael Eckfeld, Stefan Ehard, Ralf Engelhardt, Adrian Garcia, Thomas Grübler, Patrick Günzel, Klaus Heller, Julian Hörmann, Xinrui Ji, Andreas Kollmannsberger, Gerrit Illenberger, Jonathan Oelhafen, Marina Plöckl, Veronika Radlmeier, Maximilian Ronecker, Robert Setter, Maximilian Stadler, Robin Taubert, Jakob Weiland and Tobias Wolf (in alphabetic order). Thank you for the great work – per aspera ad astra!

Contact Persons
Dr.-Ing. Swen Zaremba
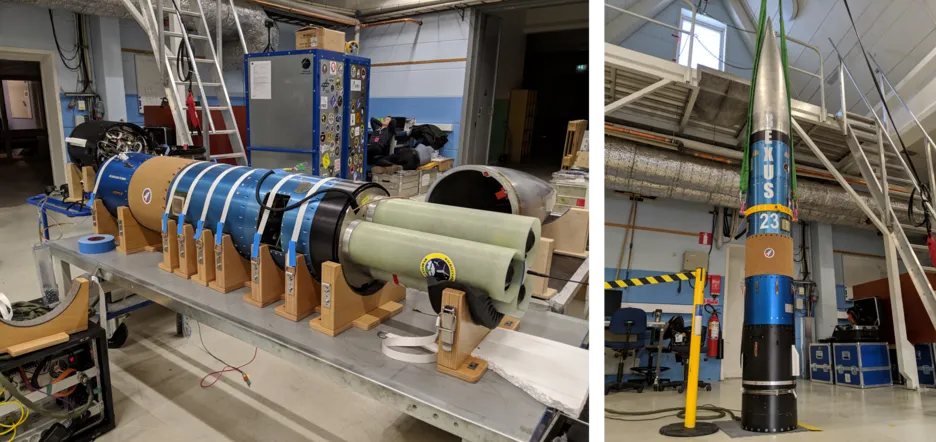